A recent analysis of UK profit warnings by EY in October 2021, found that 60% blame supply and/or cost issues, compared with 43% in Q3 2021 and just 2% between 2010 and 2020.
It's not hard to understand why. We have all become used to the benefits of a highly integrated a global supply chain, but the combined effects of a global pandemic and the unintended consequences of Brexit have both contributed to huge disruption throughout the supply chain, from manufacturers through to delivery drivers.
The headwinds are plain to see, and largely sector agnostic:
- increasing and volatile energy prices;
- skilled labour shortage;
- logistical challenges (increased freight costs, container shortages and delays);
- Brexit red tape / cost increases.
Those suppliers who are unable to absorb increasing costs will have no choice but to pass them on whenever they can. As those extra costs are passed on to the end user, the ripple effect of these inflationary pressures should not be underestimated. Higher costs will hit household budgets and potentially dent consumer confidence, derailing a recovery largely driven by the rebound in consumer spending.
Many businesses were over-leveraged and stressed prior to the pandemic. The moratorium on enforcement and myriad of government support measures (loans, HMRC forbearance, furlough) have masked much of that but, as those measures wind down and additional costs are reintroduced into monthly cash flows we expect to see an increase in distress across the supply chain, especially in those less able to absorb unprecedented increases in costs.
Stress test your supply chain
There is no magic wand that will cure market disruption, however, it is possible to anticipate evolving market conditions, and respond to them better by applying risk mitigation strategies. Do stress tests to uncover the gaps that could occur in your supply chain so you know what problems you need to solve. Identify critical relationships and distinguish between those upon which you are operationally dependent and those upon which you are financially dependent. Invest in creating added supply chain resilience and identify and reduce key single points of failure (e.g., supply concentration). Look at alternative sources of supply that can be activated, perhaps through investment in excess capacity or additional stock. Consider postponement strategies that may be sensible for your business.
Warning signs
Being able to identify and evaluate the early warnings of supplier distress will enable businesses to manage uncertainty over supplier viability. It will be important to distinguish between those businesses looking for allowances due to the short-term impact of Covid-19, and those looking for deeper concessions because their financial distress has become severe.
Stress Indicators:
- requests for price increases;
- product or service quality issues;
- lack of communication, particularly silence after persistent enquiries.
One thing is certain, early identification of stress in your supply chain and prudent intervention is key to maximise options available to mitigate risk, and to prevent under-performance becoming crisis management.
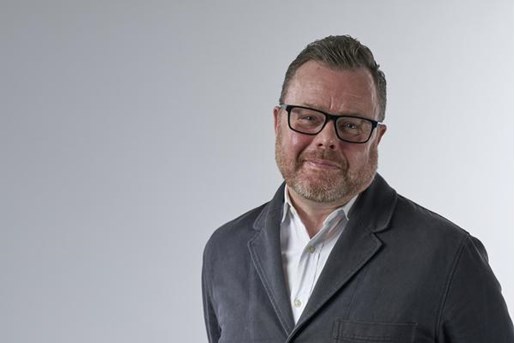
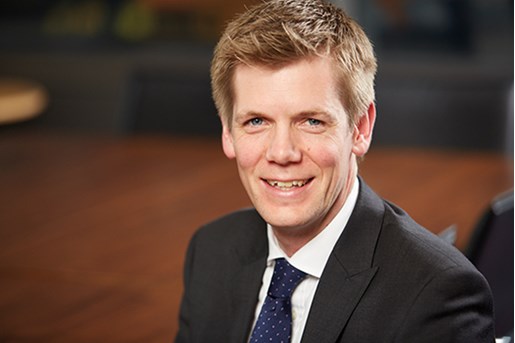